IS FIBERGLASS RECYCLABLE? PART 2 – EMERGING INNOVATIONS IN FIBERGLASS RECYCLING
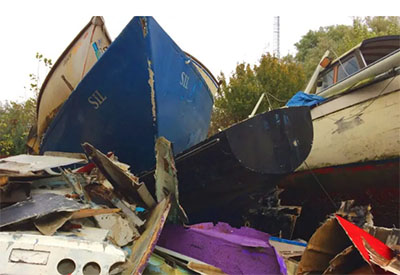
Mar 9, 2021
By Jay Weaver
Interest in finding alternative uses for used fiberglass can spark creativity and innovation. For example, a partnership involving the US, Ireland, and Northern Ireland Universities called Re-wind developed some interesting civil engineering project ideas for reusing and repurposing fiberglass blades. These include using decommissioned blades in civil engineering projects as part of powerline structures or towers, or roofs for emergency or affordable housing. In Northern Ireland, Re-wind is also considering piloting them for use in pedestrian bridges along greenways.
a recycled blade becomes a bike shelter
Further down the waste hierarchy, additional recycling options are beginning to emerge. WindEurope, representing the European Union’s wind industry, is partnering with the European Chemical Industry Council (Cefic) and the European Composites Industry Association (EuCIA) to develop new methods to reuse blade materials. The organizations estimate that 14,000 wind turbine blades will be decommissioned over the next few years in Europe alone. In May 2020, the consortium produced Accelerating Wind Turbine Blade Circularity, a comprehensive report which details design, research, and technical solutions focused on the wind turbine life cycle.
A key consideration for recycling of composite materials is to ensure that the recycling process has a net positive result compared to the alternative of disposing in landfills. One example comes from Germany, where the concept of recycling turbine blades into cement was first developed about a decade ago through a plant built under a partnership between Geocycle, a business unit of the building materials corporation HolcimAG, and the company Zajons.
How exactly is fiberglass recycling done?
There are three main processing methods are used for recycling fiberglass; grinding, incineration, and pyrolysis.
Fiberglass Grinding
This is the most obvious one, the material is chopped into small pieces and then shredded into small pieces or powders to be reused in other products. Potentially all material that can be reground can be used as recyclate; there is little or no unused waste.
The process is labor-intensive and damages the glass fibers. The recycled fiberglass material cannot, therefore, be used the same way as new glass fiber and is generally used as a filler in artificial wood, cement, or asphalt.
Fiberglass Incineration
Burning or “thermal oxidation,” is using the material to create heat for other purposes, such as making steam to power turbines that generate electricity. An unfortunate byproduct of fiberglass incineration is ash, that is usually sent straight to a landfill.
The heat content of fiberglass laminates comes from the organic materials in the resin. Most fiberglass contains only 25% to 30% organic material, so its heat content is low, and the ash content is high. Ash is primarily calcium oxide, which comes from the calcium carbonate, boron, and other oxides in the glass.
The glass fibers are generally damaged by the heat with this method too. Again this makes it a lower value material, unlike other plastics or metals that can be recycled without loss of quality.
Fiberglass Pyrolysis
This is the process of chemically decomposing or transforming material into one or more recoverable substances by heating it to very high temperatures in an oxygen-depleted environment. This is different from incineration, which takes place with oxygen. Pyrolyzed fiberglass decomposes into three recoverable substances: pyro-gas, pyro-oil, and solid byproduct— all of which can be recycled. Scrap automobile tires are disposed of by pyrolysis (the tire mountain in the United States is over 3 billion tires, growing at the rate of 250 million tires a year).
To pyrolyze fiberglass, it is shredded into 2-inch squares that are fed into the pyrolysis reactor by a vacuum assist, which also draws off most of the oxygen in the atmosphere. The reactor is then heated to around 1,4000F (7760C). At about 5,000F (2760C), the hydrocarbons in the resin decompose into gas. The gas is drawn off and sent through a scrubber, which separates it into pyro-gas and pyro-oil.
The pyrogas is very clean and has an energy content similar to natural gas. It can be sold as a natural gas replacement, and it fuels the burners of the pyrolysis reactor so that the system is self-sustaining. Pyro-oil is similar to heavy crude oil and, because of that, it has less value than normal crude oil, but it can be blended with other fuel oils or incorporated into asphalt. Pyro-gas and pyro-oil comprise about 25% of the pyrolysis traction output in roughly equal amounts. These are free of sulphur, halogens, phosphorous, heavy metals, or other elements that can cause environmental problems.
This process also does the least amount of damage to the glass fibers, making them more valuable to fiberglass manufactures.
Examples of recycling fiberglass successfully
Association for Eco Responsible Pleasure (APER) France
France was the first European country to adopt an official national recycling and dismantling network for boats. APER is a non-profit organization established in 2009 by the French Nautical Industries Federation, has established the first boat dismantling network in Europe.
A 2017 European Commission study found that 1 percent to 2 percent of more than 6 million boats less than 72 feet in length — or 80,000 boats annually — are reaching the end of life. France’s national recycling network involves 20 coastal companies and 52 dismantling sites. Its goal, aided by tax dollars, is to deconstruct as many as 25,000 boats by the end of 2023.
Boat Digest provides a helpful map of Europe with the boat dismantlers and their contact info.
Rhode Island Marine Trades Association – Rhode Island, USA
The Rhode Island Marine Trades Association is leading the way in the United States with a pilot project that repurposes end-of-life fiberglass hulls into a resource for cement manufacturers. This method has been used in Europe for the past 10 years and can be a step forward to developing more advanced recycling methods.
The process begins by stripping vessels of non-ferrous metals, engines, electronics, tanks, and interior fabrics, then sending those materials to existing recyclers. The fiberglass hull is cut up and reduced by industrial shredding equipment, and the shredded material can be used as a resource in cement products.
The ultimate hope is for sustained industry support to continue building momentum. “Right now we’re looking for people who are willing not only to give us financial and resource support but are interested in seeing how some of the functions of the recycling network and the model that we’ve created could be implemented into their day-to-day business practices and operations,” says Evan Ridley, the project manager at RIMTA.
He believes the environmental aspect, and sheer ugliness of derelicts, will drive boat recycling more than the economics. “I think it’s going to be a price that we have to pay to preserve our environment,” he says.
RITMA is also actively cleaning their marinas and harbors of floating plastic and trash, and putting a spotlight on their efforts to raise awareness of the issue.
{youtube}vWQj0u4GUeA{/youtube}
Eco-wolf – Florida, USA
Eco-wolf is a small company from Florida that produces fiberglass grinders. Wolfgang Unger is the inventor of recycling and reincorporating FRP and other natural fibers. In the 60’s he saw so much waste and scrap going into landfills and knew if something wasn’t done, there would be a big problem. As a chemist, he researched how to grind and reincorporate all the scrap fiberglass, and in 1973 he developed the method.
Wolfgang designed a machine for “harvesting” fibers that would be optimal for reincorporating into almost every production method – hand layup, spray-up, RTM, spin casting, and filament winding.
{youtube}https://www.youtube.com/watch?v=5DRw2kNIK50{/youtube}
Japan Marine Industry Association
They have developed their own recycling program in 2005, as the country was faced with a large number of illegally dumped fiberglass boats. The program uses the existing vehicle and boat dismantlers, and cement plants as recycling facilities. It has 414 boat dealers and marinas, 36 dismantlers, nine processing companies, and five cement plants in its network.
The program has recycled more than 8,000 vessels since 2005 and reportedly sends only 12 or 13 percent of the material to landfills. The cost to transport and recycle the vessels falls on the boat owner, and many opt for cheaper dismantling because of the high cost of landfill dumping. The government support is promising in a country with limited space for landfills and a marine-reliant economy.
Zagons Logistik – Germany
The world’s only industrial-scale reprocessing of windturbine blades is currently undertaken by Zagons Logistik at its factory in northern Germany.
On-site, when the wind turbines are dismantled, the company’s service begins with the use of a mobile saw that originated in the concrete and mining industry. It uses a cable with diamond inserts, and a water mist to cut large blades into shorter sections of 35-40 feet long. These sections can then be transported on a conventional truck rather than a longer vehicle requiring a police escort.
At the reprocessing facility, a stationery cable saw is used to reduce blade sections further, to about three feet in length. These sections then enter a crusher that has been modified to handle fiber-reinforced plastics. This reduces the material size to about 1-2.5 inches.
The next stage sees the material being fed into a cross-flow shredder, which rotates 800 rpm, reducing the chunks of waste blades further. A hammer mill then takes their size down to a maximum of 0.5 inches, after which they are mixed with other, wet waste materials. The addition of wet substances ensures that glass fibers from the crushed turbine blades are captured and bind to the rest of the mixed waste.
The result is a compound that cement producer Holcim can use both as a substitute fuel, replacing coal-ash, and as raw material, displacing some of its need for virgin washed sand.
Zagons Logistik is eager to secure larger volumes of waste turbine blades since its plant is running only at about one-third of its full capacity. The company currently reprocesses about 400-500 tonnes of waste turbine blades each month.
Plasti-Fab Washington, USA
Plasti-Fab, a manufacturer of fiberglass composite solutions, has begun large-scale integration of its recycled fiberglass reinforced plastic (FRP), reducing negative emissions, the use of non-sustainable materials, and raising industry standards for greener production.
For the last 40 years, Plasti-Fab has been involved in fiberglass production, mostly due to its use of fiberglass reinforced plastic (FRP) composites. Plasti-Fab’s recent acquisition of custom-made equipment for large-scale recycling raises the standard for reducing environmental impact in fiberglass-based production.
Their new grinder machine allows Plasti-Fab to collect various wastes, trim, and overspray materials that can create a compound reused in several closed mold manufacturing processes. The production not only cleans up the production process but also results in a recycled material that can replace previously used non-biodegradable foam core.
American Fiber Green Products – Florida,USA
From their newer plant in Florida, American Fiber Green Products recycling entity, Amour Fiber Core, is transforming old fiberglass into wood-substitute planks that go into picnic tables, fencing, seawalls and more. Amour takes fiberglass from boats, car and truck bodies, personal watercraft, shower stalls, and other fiberglass wastes, then recycles all into high-strength, durable commercial and consumer products. This Florida company will take old boats (for a fee), and most locations have a pick-up service.
Isodan has developed a unique dust free and mobile production plant solution for recycling of fiberglass and composite waste materials. The Isodan plant can handle all kinds of fiberglass and composite materials such as wind turbine blades, decommissioned boats and industrial waste materials.
Built in a shipping container, the whole operation can be transported like a normal container, to anywhere in the world. It can be operated by just one person and it will recycle fiberglass panels, mat, and other materials too.
{youtube}https://www.youtube.com/watch?v=KR26ol6zo1c{/youtube}
Global Fiberglass Solutions – Denmark
Founded in 2009 by Don Lilly and Ken Weyant, GFS started looking at wind turbine blades as a recycling feedstock. With Composite Material & Engineering Center at Washington State University, they developed a patented process for recycling fiberglass composites.
Now, GFS is going through design, engineering, site preparation and air quality permitting for its scale-up in Sweetwater, Texas. The facility is currently capable of processing two or three blades per day, or 2-3 tons per hour on an eight-hour shift. At full production, the plant will be able to process eight tons per hour, or about one blade an hour.
GFS leaders see an ample supply of feedstock. Between earlier generations of wind turbine blades reaching old age and government tax credits incentivizing upgrades to more efficient blades, a lot of material is projected to enter the end-of-life stream in coming years.
As far as wind turbine blades are concerned, GFS charges system owners to collect decommissioned blades. The turbine owners would otherwise have to pay for collection and landfilling. Some counties are already banning turbine blades from their landfills, Englund noted.
Additionally, the company is working to commercialize the recycling of carbon fiber composites. GFS helped fund research by a WSU team developing a chemical recycling method for the materials, which are used in the aerospace, energy, and other industries.
But GFS is also looking beyond wind turbine blades to scrap fiberglass from boats and planes.
“There’s a lot of stuff going to our landfills right now that are glass fiber composites,” says Karl Englund, chief technology officer for Global Fiberglass Solutions. “We’re really focused not just on the wind turbines but all the other fiberglass streams out there too.”
Making new boats with recycled fiberglass
Ryds båtar is a Swedish boatbuilder, producing about 3,600 small powerboats each year in 36 models ranging in size from 11 to 20 feet, so Ryds goes through a lot of fiberglass. About six years ago, with the help of the Swedish Institute of Composites, Ryds began development on manufacturing boats with closed-loop recycled scrap, which accounted for about 10% of its layup production. The result was a 15.5-foot concept boat, containing about 20% recycled fiberglass by weight.
The original single-skin laminates of sprayed-polyester fiberglass in the hull and deck were cut back by 50% and replaced with a sprayable polyester mixture containing 33% to 40% ground scrap. Core materials, such as plywood, Coremat, and Divinycell, were replaced with the scrap mixture. The boat’s laminates had equal or better strength in all respects and, where the recycled compound replaced plywood, screw-holding power improved significantly.
In the end, the goal of increasing innovation towards additional use applications for retired fiberglass boats, wind turbine blades, and aircraft parts requires having enough market demand to incentivize the creation of facilities that can recycle the material. Alongside that challenge is a lack of policy in the U.S. regarding end-of-use considerations for turbine blades, further contributing to the status quo of storage or disposal as solid waste in landfills.
A rising tide lifts all boats.
While we still don’t have a definite answer for the boats in much of the USA, as the fiberglass recycling industry grows for the wind turbines, there will be more options for the marine sector.
An added approach to the blade recycling issue is to focus on the upfront piece and that’s what the blades are made of. Additional research and development are looking into using thermoplastic resin instead of fiberglass or carbon fiber for wind turbine blades. The material may be easier and cheaper to recycle.
Its aim: to validate the processes for using Elium® as a turbine blade material. Effiwind took a decisive step forward at the end of 2016 when it produced the first 25-meter blade. NREL’s thermal welding technique—coupled with Arkema’s resin system—earned a 2020 Special Recognition Award from R&D 100 for being a “market disrupting” technology.
Two approaches to a more circular economy are greater communication along the wind turbine supply chain and ambitious goals. For example, Vestas Wind Systems A/S, a wind turbine design, manufacturing, and global installation company, announced a bold commitment to producing zero waste wind turbines by 2040.
The company plans to achieve this by increasing recyclability over the next 20 years by working closely with its partners along the supply chain to ultimately avoid any incineration or landfilling of its products. More partnerships like these between wind industry companies are needed to help fill the gap and make wind energy systems 100 percent recyclable.
{youtube}https://youtu.be/KR26ol6zo1c{/youtube}
Finally, I found this interview interesting, it’s about the pyrolysis method of fiberglass recycling.
About the author
Jay Weaver, 33, grew up sailing with his Dad in Michigan, and recently restored his 1968 Columbia 22 that he sailed on Muskegon Lake and Lake Michigan. Currently living in El Salvador, he became much more aware of the environmental impact of plastic pollution in nature and the ocean.