MarsKeel Uses Dissimilar Metal Combination Keel For 76-Foot Yacht
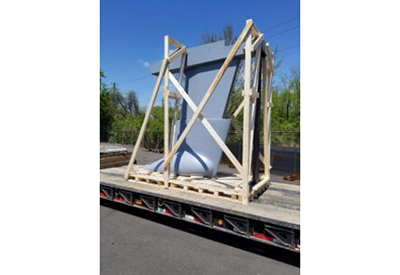
Sept 13, 2022
Working alongside a US-based designer and boat building company, Burlington ON-based MarsKeel Technology recently provided a dissimilar metal combination keel for a 76-foot yacht. The keel consists of two sections; the upper section is a hollow fabricated steel keel fin (A36/44W) and the lower section is a lead cast bulb.
The bulb was integrally cast onto the fin, which is a hallmark of MarsKeel. An Integrally Cast Bulb (ICB) simplifies the connection between the fin and the bulb. This process has a lower leg on the fin that extends into the bulb making a very secure attachment between the two parts.
This project was a collaboration between MarsKeel, Stephens and Waring Yacht Design, and Lyman-Morse. The designer on the project, Stephens and Waring Yacht Design, offered the construction drawings for both the fabricated keel fin and the lead casting.
Stephens Waring Yacht Design is a custom naval architecture and engineering firm located in Belfast, Maine. MarsKeel has a longstanding relationship with them, and over the years, we have collaborated on several similar projects.
Lyman-Morse is a world-renowned yacht builder for sailing and motor yachts as well as a repair facility in both Thomaston Maine and Camden Maine.
Product Specifications
The upper hollow steel fabricated fin weighed approximately 1,996 lbs, while the lower cast lead section of the lead cast bulb weighed 14,824 lbs. The relatively light upper section allowed the centre of gravity of the keel and yacht to be lowered, creating a higher level of stability for a given weight and draft. There was an FRP foil added to the upper section of the keel. What you can see above the lead is the fabricated and machined steel structural portion of the keel above the lead line. The top of the keel is not lead to allow for a lower CG and an overall lighter keel with the same stability.
The top ‘Tee’ section of the keel holds the needed keel bolts, which cannot be seen from the ground. This section fits into a precise recess in the bottom of the boat, so the sides of the Tee needed to be CNC machined after fabrication and stress relieving to ensure that they were straight and parallel.
The yacht captain came to the shop to inspect and detail the fin before it was cast onto the bulb. The keel then proceeded into the set-up stage, where the fin was positioned in the mold at the correct height, angle, and other specifications. It was checked from all angles as well as from inside the mold, before the second side of the mold was closed. This is done roughly by the mold positioning the fin using the casting neck of the mold, and the fine positioning is then checked by referring to the keel head. This is where a team with decades of experience really makes a difference. It is only ready to be cast after the head of casting and the plant manager are happy with the position. Once the fin is in the correct position it is secured to the mold so that it can not move at all during the pouring process.
What made this project complex was the connection between the two materials. With the combined experience of MarsKeel, the designer, and the builder, we were able to overcome challenges and create a safe and simple design.